Fiberglass Boat Modification & Fabrication in Seattle
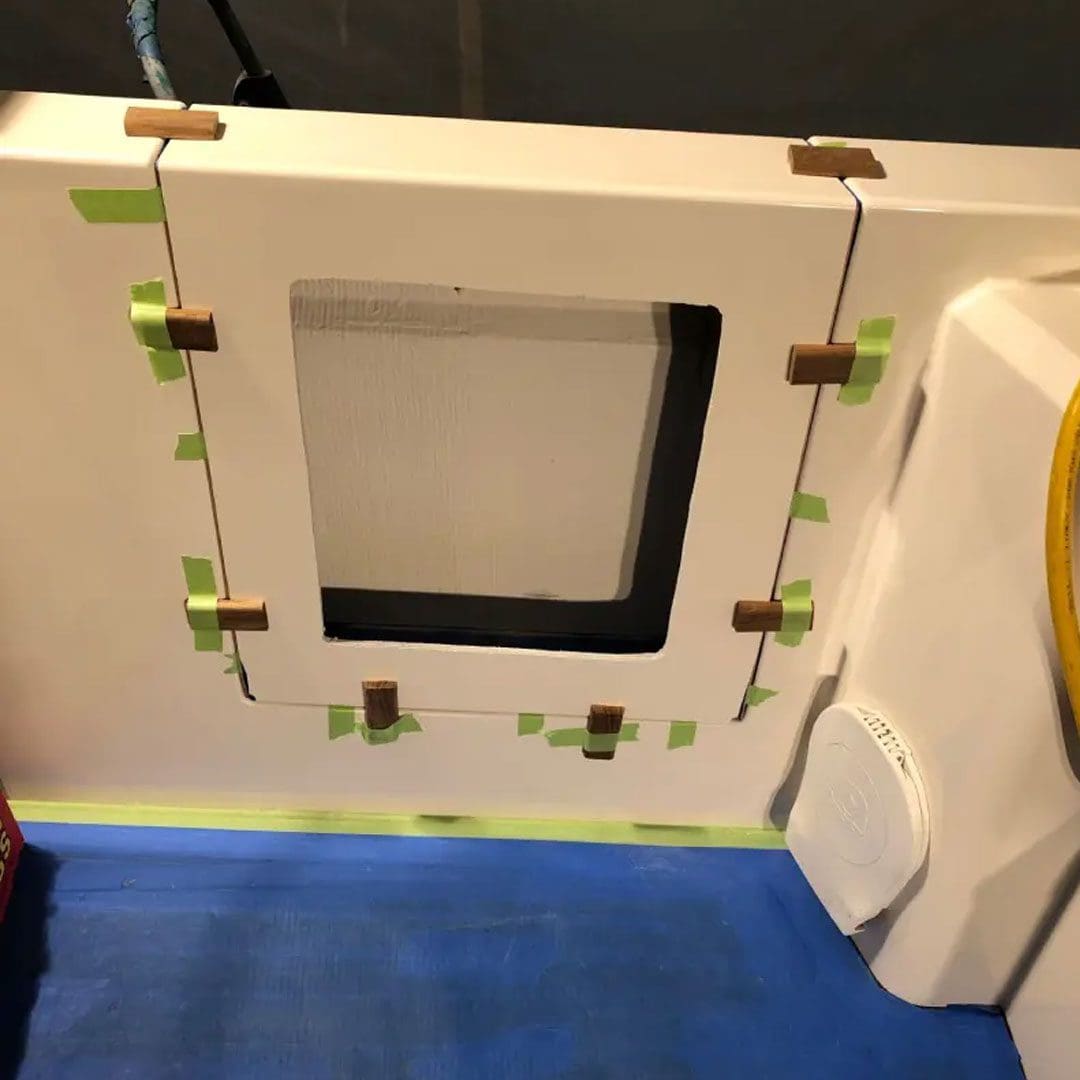
Fiberglass boat modification
Many of our customers are happy with their boat but over time find that it lacks some features that would make their boating experience more comfortable or enjoyable. Rather than look for a new boat with the features they want, they choose to modify their boat.
At Northwest Marine Fiberglass our expertise in fiberglass construction, and fabrication methods and materials has allowed us to make a variety of changes to boat hulls, decks, and bottoms to accommodate our customers’ needs, that are structurally sound and blend perfectly with the rest of the vessel. Following are a couple boat modification examples.
Bulwark gates
Many boats include a door in the transom leading to a swim platform that allows access to the cockpit from the dock without climbing over the side. A bulwark gate cut into the side of the boat allows access straight from the dock without the sometimes-tricky maneuver of stepping over lines and around a corner to get from the dock to the swim platform to get to the transom door.
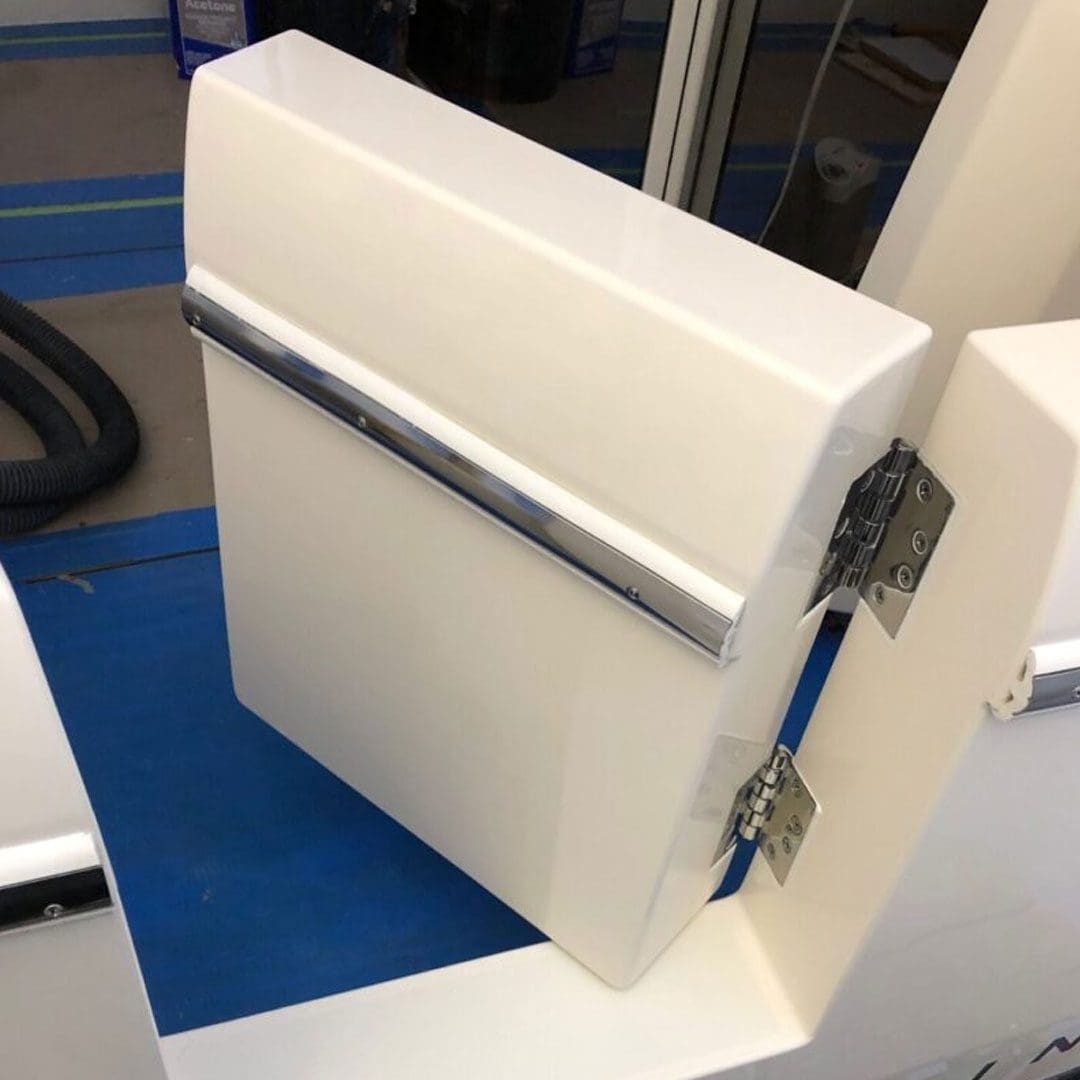

Process
Care is taken when choosing the precise location of the cutout. Cosmetic details like joints in a teak cap rail are taken into consideration. There must be enough room for the door to swing inboard, clearing the cabin house to lie flat against the inboard face of the bulwark. When the cut is made extreme care must be taken to make a clean cut, as the cutout section of the hull will later be used to build the door. The opening needs to be built up and reinforced since it is a critical structure of the hull and must handle the weight and operation of the hinged door. When the opening is complete the cutout section of hull is fastened back into position so that it lines up perfectly on the outside, the opening is sheathed in a spacer, and becomes the mold for the new door. The end result is a door with a perfect fit that blends seamlessly with the rest of the hull. Every boat is different, but a typical bulwark gate installation will take four to six weeks and cost around $16,000.
Bow Thruster Installation
Another popular boat modification is the addition of a bow thruster. A bow thruster makes the close-in boat maneuvering required during docking much easier. Hard core old salts sometimes scoff, but for recreational boaters the whole point of being out on the water is to relax and enjoy themselves, and anything that makes the experience less stressful and more enjoyable is a welcome feature. At Northwest Marine Fiberglass we get a lot of requests for bow thrusters and have become experts at this structural hull modification.
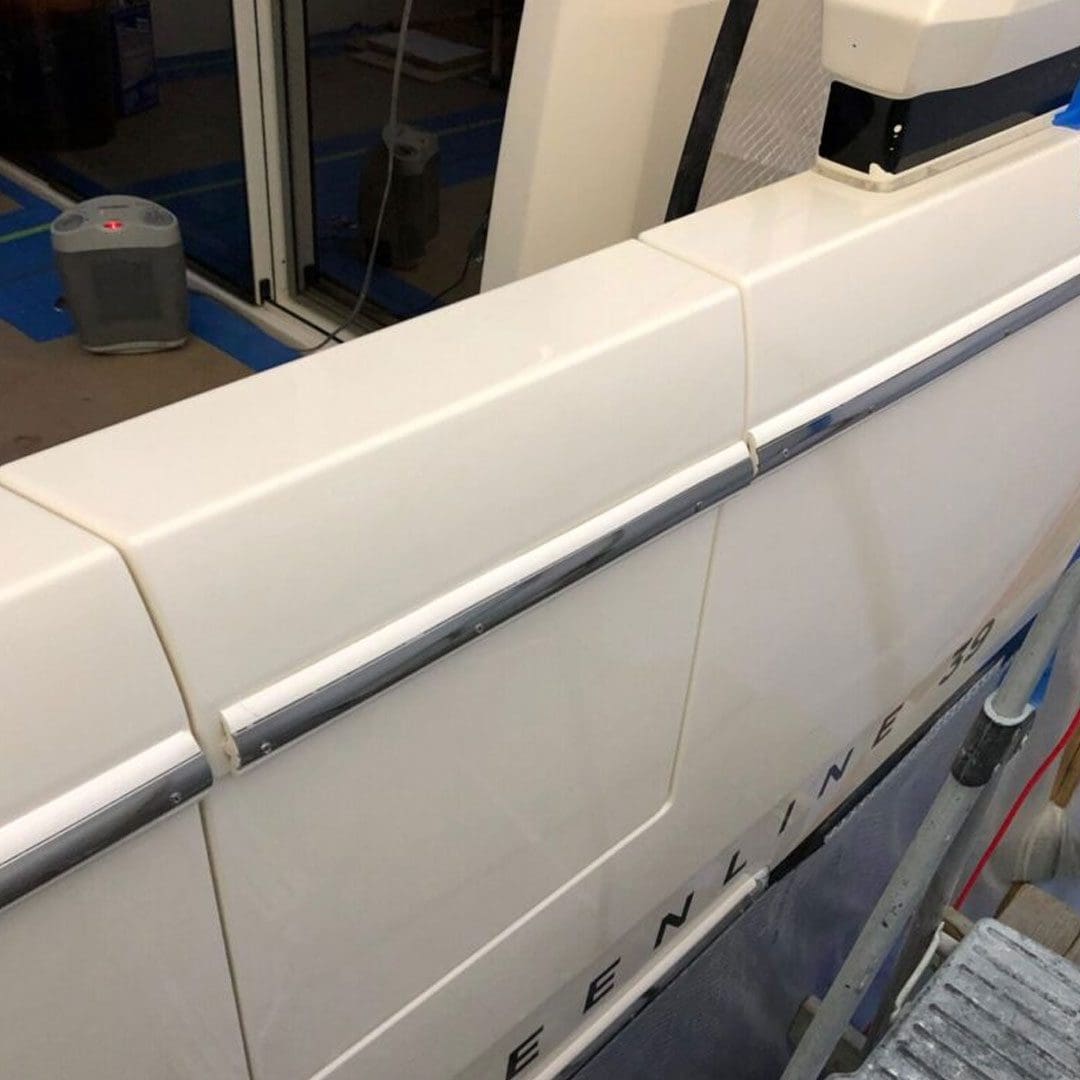
Process
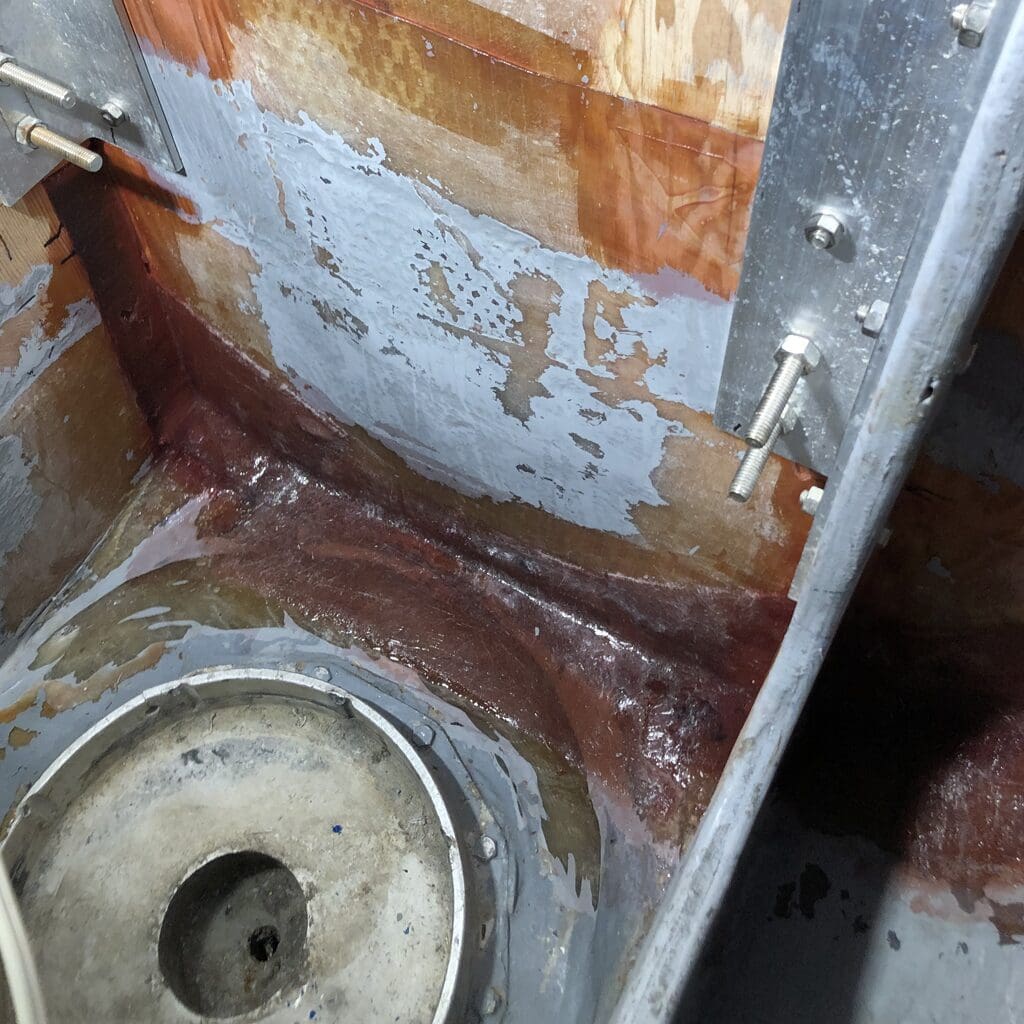
The first step is to gain access to the location of the tunnel on the inside of the boat
This can be as simple as removing a mattress, removing the top of a v-berth, and cutting out a plywood sub floor, or as difficult as doing all of the above, then needing to shorten drawers to make room for the motor, and cut through two main fore and aft stringers. We once had to Remove a chain locker bulkhead, two fore and aft bulkheads, cut back a floor, and cut and remove a balsa core to create the space on the hull to cut a hole with enough room around it to glass in the tube. Then,all the structure that was removed had to be rebuilt.
Determining the precise location of the tunnel is critical
Manufacturers requirements that affect performance like the length of the tunnel and the distance below the waterline must be considered along with equipment dimensions like the height and diameter of the thruster motor that affect the installation of the unit in the boat. At Northwest Marine Fiberglass we recognize that a bow thruster is not a small expense, and the boat owner has is excited and has high expectations. We focus on picking the precise spot that results in optimum performance. In the end hull shape and interior construction leave you working with limited options, but in almost every case a matter of moving the pilot hole for the cut out an inch in one direction or another leads to the best possible performance.
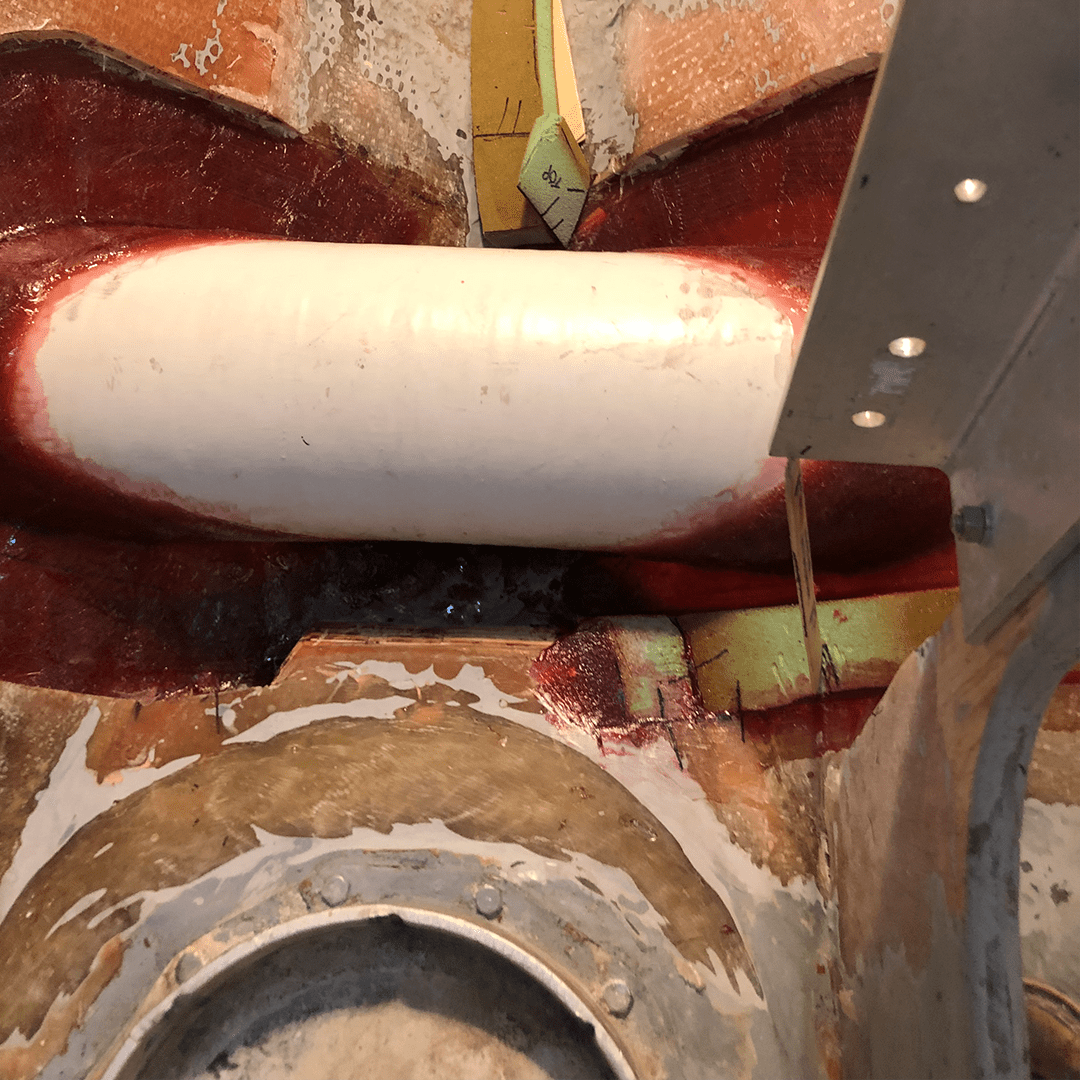
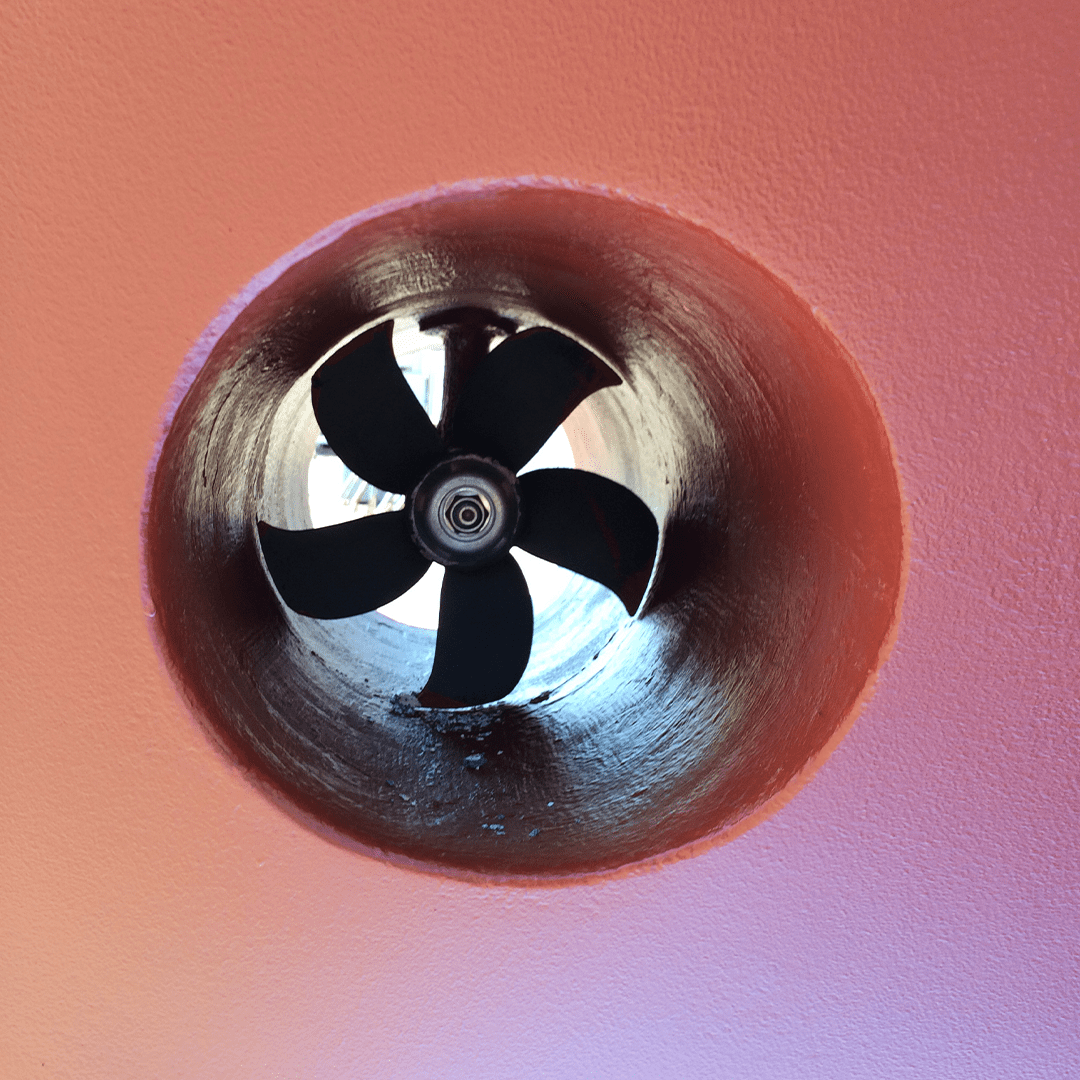
Vessel protection and dust containment are important
If you do a perfect jobbut leave the inside of the boat contaminated with itchy fiberglass dust, or damage finishes with splattered resin or spilled acetone, you are not going to have a happy customer. Before getting into the messy cutting, grinding and glassing we take time to protect the vessels interior. Cushions and personal belongs are removed. Floors, walls, and doorways are covered in protective films, and a visqueen grinding sack, attached to a dust extractor and equipped with a vacuum hose is set up. Any passageways leading to other parts of the bilges are plugged.
Hull strength must be maintained
When cutting a large hole and glassing in a tube the structural integrity of the hull must be maintained. At Northwest Marine Fiberglass we always glass to the bare hull, never to a cored hull. If there is core in the tube location, we remove it down to the solid glass hull, allowing at least a four inch border around the perimeter for tabbing in. Our fiberglass lay up is beefy, often as thick as, and sometimes thicker than the hull itself. The tube gets glassed from the outside as well.
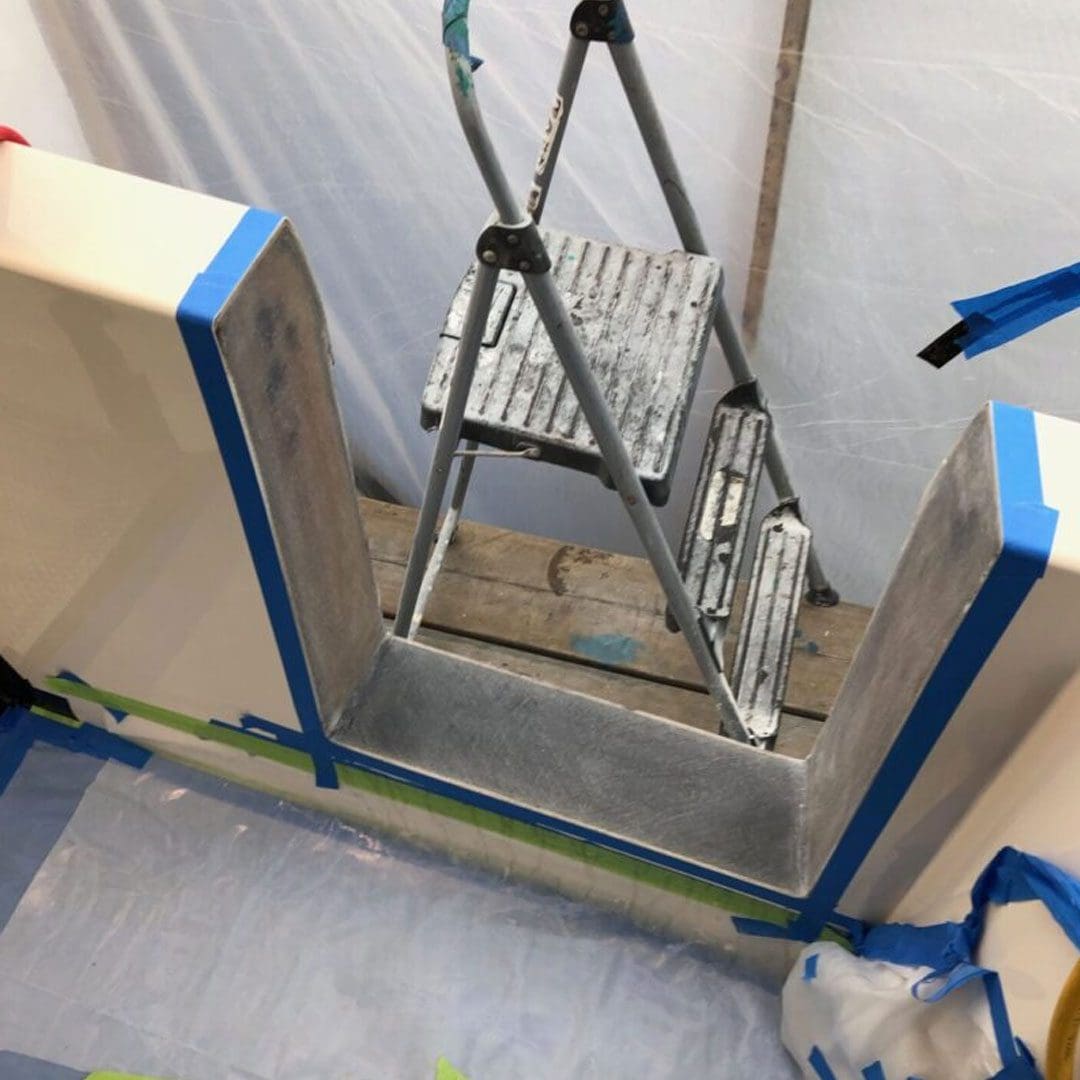

Looks matter to us
Although it’s a structural part of the boat that is rarely seen we are proud of our work. We do a quick sanding to eliminate any spikes of fiberglass, match the color, and gelcoat all of the interior glass work to blend it with the rest of the bilge. On the outside of the boat we fair our work, leaving a neat and uniform radius around the tunnel opening, and seal it with Interlux 2000-E epoxy barrier coat before touching up the bottom paint.
Cost
As explained, every boat is different, requiring more or less work to gain access. Determining location, laying down vessel protection and providing dust containment, cutting the hole, glassing in the tube inside and out, and doing the finish work can usually be done in a little over a week and cost between $5,500 and $6,000. Gaining access and rebuilding what was removed for access are the variables that determine the end cost. We have done thruster tunnel installations for as low, as $4,500 and as high as $14,000.
Bulwark gates and bow thruster tunnels are only two examples of hull modifications we do. We install stern thrusters, sonar tubes, Sea keeper Gyro Stabilizer structures, storage bins, live bait wells and crab tanks, and cockpit extensions.


Custom fabrication
Sometimes our customers want to make an addition to their boat that requires building a mold and fabricating a custom fiberglass part. We build and install custom molded fiberglass hardtops, swim platforms, hard dodgers, storage cabinets, and seating arrangements. We have enclosed pilothouses with molded fiberglass bulkheads with custom windows and doors to replace canvas enclosures.
At Northwest Marine Fiberglass we work closely with the boat owner to ensure that the new addition is built to their individual needs, considering their height and sight lines for example when building a hard dodger for a sailboat, or a back wall for a sport fisherman.
Our knowledge of mold making and fiberglass construction methods and materials, along with our understanding of the importance of aesthetics, leads to an addition to the boat that looks like it was always a part of vessel and is tough enough to hold up over time.
The process
Our fiberglass parts are quite different from on another with complications and variables, but all share the same basic process. A swim platform is a good example.
Patterning Making
First a pattern is made on the boat, matching the camber of the transom, laying out the desired shape, and marking the locations of support brackets, swim ladders, cleats, staples, and any other hardware the owner wants to have on the new platform.


Mold Making
The pattern is used as a guide for building the mold in the shop. A dam is set up around the outline of the platform on a sheet of wet sanded and buffed melamine.
Corners are formed, and a wax radius is formed around the perimeter. After waxing with mold release wax and spraying on PVA mold release the inside of the mold is ready.
Building the part
Several coats ofcolor matched gelcoat are sprayed into the prepped mold and allowed to cure overnight. Next a skin coat of ¾ ounce fiberglass mat is laid up on top of the gelcoat and allowed to fully cure. Carefully patterning, cutting labeling and organizing the fiberglass cloth that will form the outer skin of the platform ensures the layup process goes smoothly, using the correct amount of catalyst for the ambient temperature ensures enough working time while still ensuring a full cure.


The next step is the internal structure of the swim platform
PVC foam is used overall as a core material, with high density Coosa Board fiberglass reinforced composite board in areas where hardware will attach. ¼ inch aluminum is installed on top of ¾ inch Coosa board to match the height of the 1inch foam core. Everything is laid out, patterned, cut, and installed in the molded fiberglass shell with a fiber reinforced structural filler.
The bottom fiberglassskin is laid up, and the part finished
The bottom skin uses the same process as the top skin, only with about half as many layers. The part is then popped out of the mold, the edges are trimmed, and the surface is wet sanded and buffed to a high gloss, and to eliminate any surface imperfections. Nonskid panels are laid out, masked and sanded, and nonskid is applied, most often Awlgrip-Giptex. Finally, all the hardware is installed. The end result is a brand-new part that looks like it came out of the factory with the boat.

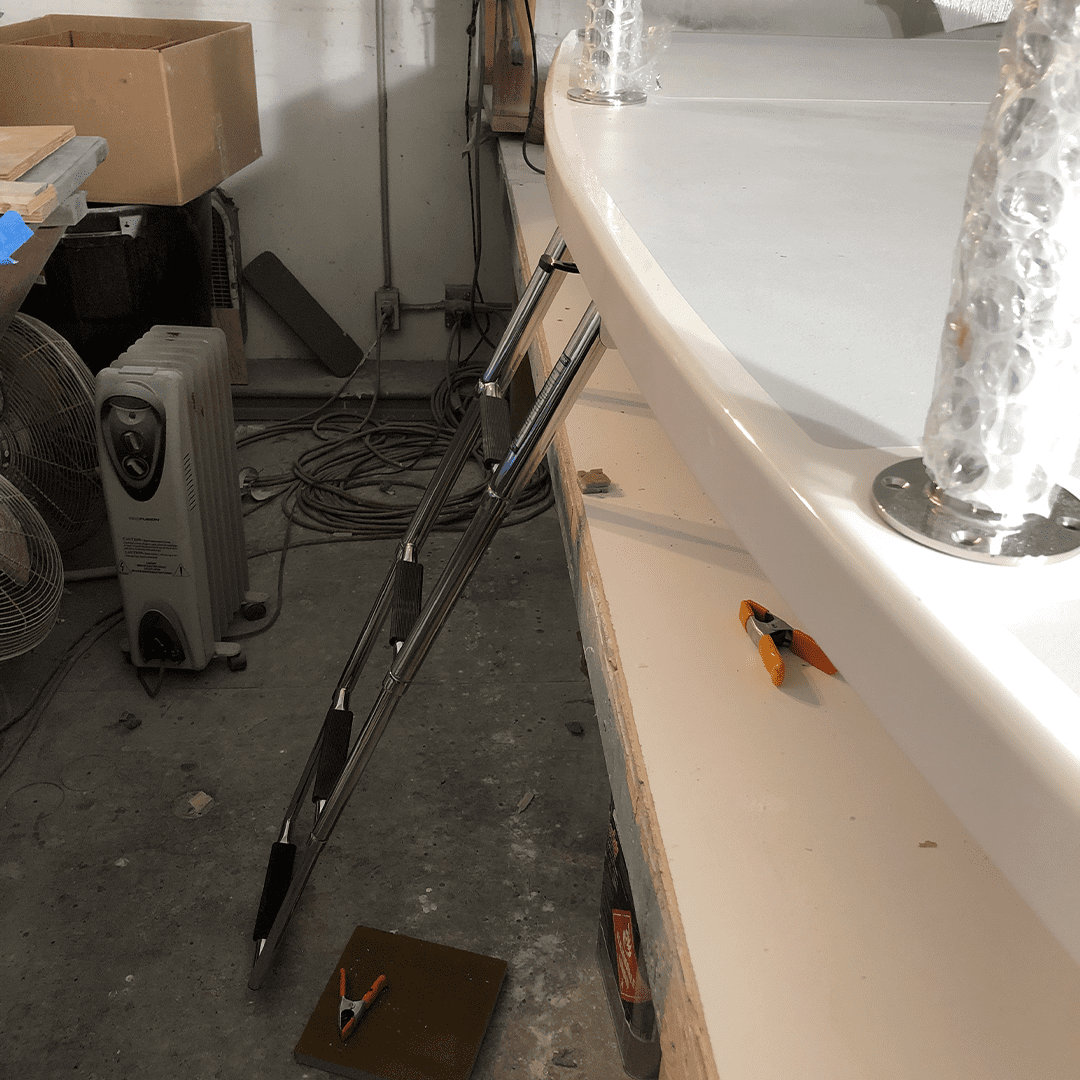
Installationtakes less than a day
Due to thoughtful planning from the start, we rarely encounter problems during an installation
Cost
Swim platforms vary in size and details, but a common price for a 12 ft long 3 ft wide swim platform would be around $13,000. Other types of fabricated parts vary so widely that it isn’t really possible to say what a custom fabricated fiberglass part costs. They really need to be estimated on an individual basis.
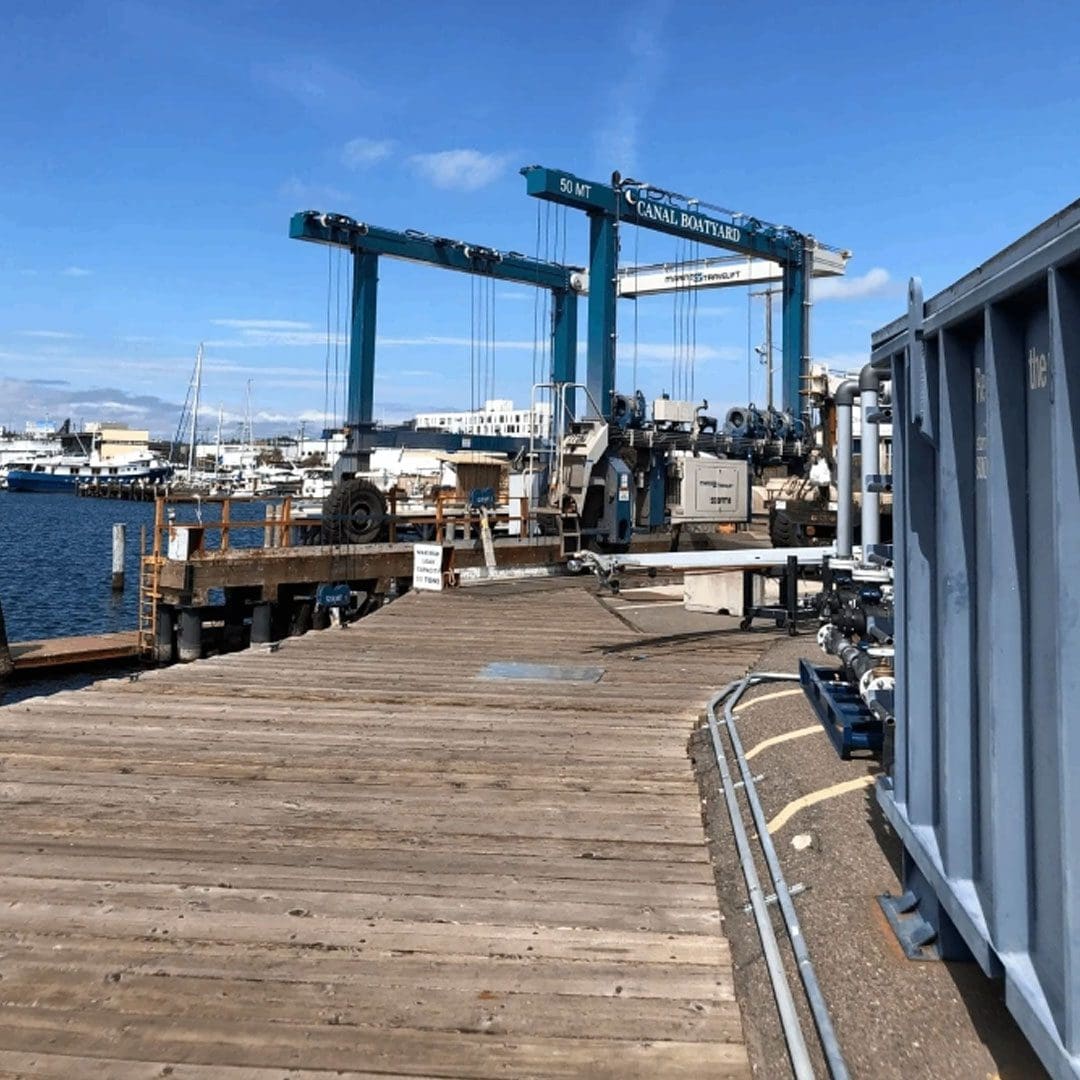
FAQ
We do the following boat modifications: Bulwark gates, transom doors, bow thruster tunnels, custom seating, hatch installations, bait wells and crab tanks, cockpit extensions, sonar tubes, and gyro stabilizer mounting pads.
We build the following custom molded fiberglass parts: Hardtops, hard dodgers, pilothouse enclosures, swim platforms, deck storage boxes, cockpit cabinets.
A boat modification or custom fabricated fiberglass part done by Northwest Marine Fiberglass will blend seamlessly with the rest of the boat. The color will match perfectly, and because we take care to follow the lines and style of the vessel in any change we make to the hull or deck, there will be no indication that the boat didn’t come out of the factory that way.
We do several different types of boat modifications and build several different custom fiberglass parts, and cost depends on the size and complexity of the project.
Following are a few examples:
Bow thruster tunnel with easy access | $4,500. |
Bow thruster tunnel involving major tear out and rebuilding of interior structure. | $14,000. |
3’x9’ swim platform with swim ladder and two staples using existing supports. | $11,000. |
4’x 16’ swim platform with new supports, swim ladder, and four staples. | $15,000. |
Hardtop for a 65’ power boat, installed. | $65,000. |
Hardtop for 40’ power boat. | $47,000. |
Bulwark gate or transom door. | $13,000 to $16,000. |
We use isophthalic polyester resin and a combination of fiberglass mat and 1708 biaxial weave fiberglass cloth in our hull and deck modifications and custom molded parts. In cored areas we use PVC foam core, and in places where hardware mounts, Coosa Board fiberglass reinforced composite board. For fairing we use 3M vinyl ester fillers and Awl Fair, Maas,West system, and System3 epoxy fillers. The finished surface is either a polyester gelcoat finish, or and epoxy primer and LP topcoat finish. We use Awlgrip and Alexseal topcoat systems.
Working owner Paul Ziegler has over forty years of experience doing hull modifications and building custom fiberglass parts,beginning with cutting off and replacing bows of boats using melamine forms and quick molds taken from identical boats bows in the early 1980s, and re-forming the entire starboard side of a Baba 40’ in 1989. In the 1990s there were several cockpit extensions on 60’ plus powerboats as well as plug, mold, and boat building at Yachtfish Marine in Seattle. For the past 24 years as owner of Northwest Marine Fiberglass Paul has continued doing a variety of boat modification and custom fabrication projects. They are some of the more challenging and enjoyable jobs he’s involved in.
We guarantee that our hull or deck modification or molded fiberglass part will not develop problems and will hold up as well as, or better than the rest of the vessel. We have never had a customer come back, even after many years, and say that a crack had appeared in any of our work, or that a core had become unbonded, but if it happens within five years, we will repair it without charge. That does not include failure due to a collision or some other mishap.
For an estimate:
Hit the Get in touch button on any page on the website or click here to contact us
Email us at [email protected]
Or call (206) 423-7683